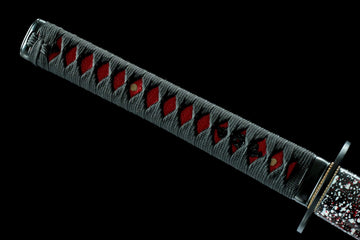
,文章长度约1000词左右
html
Japanese Handcrafted Blades: The Art of Traditional Swordsmithing
For centuries, Japanese blades have been revered worldwide for their exceptional quality, beauty, and craftsmanship. The art of creating handmade Japanese blades is a tradition that dates back over a thousand years, blending metallurgical expertise with spiritual dedication. These blades are not merely weapons or tools but represent the pinnacle of artistic expression in metalwork.
The History of Japanese Bladesmithing
The origins of Japanese swordsmithing can be traced to the Kofun period (300-538 AD), when the first curved blades appeared. However, it was during the Heian period (794-1185) that the iconic katana began to take shape. The tumultuous Sengoku period (1467-1615) saw unprecedented demand for high-quality swords, leading to the golden age of Japanese swordsmithing.
Several famous schools emerged during this time, each with distinct characteristics:
- Yamato-den: Known for powerful, practical blades
- Yamashiro-den: Produced elegant, refined swords
- Bizen-den: Created durable blades with beautiful grain patterns
- Soshu-den: Combined techniques from various schools
- Mino-den: Developed unique tempering patterns
The Traditional Swordsmithing Process
Creating a traditional Japanese blade is an incredibly labor-intensive process that can take weeks or even months to complete. Master smiths follow time-honored techniques passed down through generations:
1. Tamahagane Production
The process begins with creating tamahagane, the special steel used in Japanese blades. Iron sand is smelted in a tatara furnace for three days and nights at extremely high temperatures. The resulting steel contains varying carbon content, which the smith carefully selects and combines.
2. Forging the Blade
The smith repeatedly folds and hammers the steel to remove impurities and create thousands of layers. This process:
- Distributes carbon evenly
- Creates the distinctive grain pattern (hada)
- Removes slag and bubbles
- Strengthens the steel
After shaping the basic form, the smith applies a special clay mixture to the blade before the final heat treatment.
3. Differential Hardening (Yakiba)
The clay-coated blade is heated and then quenched in water. This creates:
- A harder edge (ha)
- A softer spine (mune)
- The characteristic curvature (sori)
- The beautiful hamon (temper line)
4. Polishing and Finishing
A skilled polisher (togishi) spends weeks bringing out the blade’s beauty using a series of increasingly fine stones. This process reveals:
- The hamon pattern
- The steel grain (hada)
- The blade’s geometry
- Any structural flaws
Keyword: Handmade Japanese Blades
The Spiritual Aspect of Bladesmithing
Traditional Japanese swordsmithing is as much a spiritual practice as it is a craft. Smiths often:
- Purify themselves before work
- Wear white Shinto robes
- Maintain a sacred workspace
- Consider the sword’s soul (tamashii)
<p