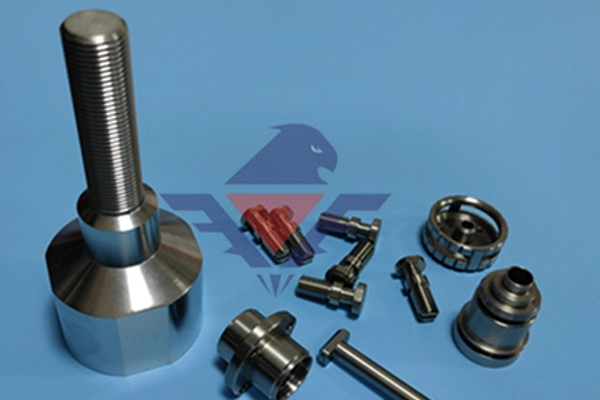
# Swiss Machining: Precision Engineering for Complex Components
## The Evolution of Swiss Machining
Swiss machining, also known as Swiss screw machining or Swiss turning, has revolutionized the precision manufacturing industry. Originating in Switzerland during the late 19th century for watchmaking, this advanced machining technique has evolved to become indispensable across various high-tech industries.
## How Swiss Machining Works
Unlike conventional lathes, Swiss machines utilize a sliding headstock and guide bushing system that provides exceptional stability during machining operations. This unique design allows for:
– Extreme precision with tolerances as tight as ±0.0001 inches
– Superior surface finishes
– Reduced vibration during cutting operations
– The ability to machine long, slender parts that would otherwise deflect
## Key Advantages of Swiss Machining
### 1. Unmatched Precision
The guide bushing system supports the workpiece close to the cutting tool, minimizing deflection and enabling exceptional dimensional accuracy even with complex geometries.
### 2. High Production Efficiency
Swiss machines can perform multiple operations simultaneously, including turning, milling, drilling, and threading, significantly reducing cycle times compared to traditional methods.
### 3. Material Versatility
These machines handle a wide range of materials effectively, from plastics and aluminum to exotic alloys and hardened steels.
Keyword: Swiss Machining
## Applications Across Industries
Swiss machining has found critical applications in numerous sectors:
– Medical: Surgical instruments, implants, and dental components
– Aerospace: Precision fittings, hydraulic components, and fasteners
– Automotive: Fuel injection systems, sensors, and transmission parts
– Electronics: Connectors, contacts, and miniature components
– Defense: Firearm components and optical systems
## Choosing the Right Swiss Machining Partner
When selecting a Swiss machining service provider, consider these factors:
– Experience with your specific industry requirements
– Quality certifications (ISO, AS9100, etc.)
– Material capabilities
– Secondary processing options
– Prototyping versus production capabilities
## The Future of Swiss Machining
As industries demand increasingly complex and miniaturized components, Swiss machining continues to evolve with:
– Advanced CNC controls
– Multi-axis capabilities
– Automated loading systems
– Integration with Industry 4.0 technologies
– Improved tooling materials and coatings
For manufacturers requiring high-precision, complex components with tight tolerances, Swiss machining remains the gold standard in precision engineering. Its ability to produce intricate parts efficiently makes it an essential technology for modern manufacturing challenges.