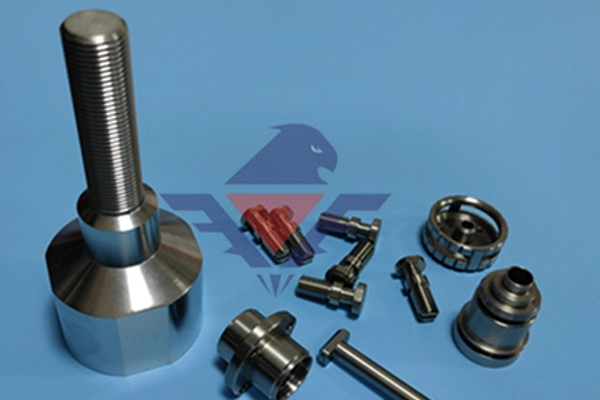
,文章要符合SEO优化,字数在1000字左右
html
Precision Swiss Machining for Complex Components
In the world of manufacturing, precision is paramount. When it comes to producing intricate, high-tolerance components, Swiss machining stands out as a superior solution. This advanced machining technique enables the creation of complex parts with unparalleled accuracy, making it indispensable for industries such as aerospace, medical, and electronics.
What is Swiss Machining?
Swiss machining, also known as Swiss screw machining or Swiss turning, originated in Switzerland’s watchmaking industry. This precision machining process utilizes specialized CNC Swiss-type lathes that combine turning and milling operations to produce small, intricate parts with tight tolerances.
The key differentiator of Swiss machining lies in its unique guide bushing system. This innovative feature provides exceptional support for the workpiece close to the cutting tool, minimizing deflection and vibration. As a result, Swiss machines can achieve tolerances as tight as ±0.0001 inches (0.00254 mm), far surpassing conventional machining capabilities.
Advantages of Swiss Machining
1. Exceptional Precision
The guide bushing system and sliding headstock design of Swiss machines allow for machining operations very close to the support point. This setup dramatically reduces tool pressure and workpiece deflection, enabling the production of parts with extremely tight tolerances and superior surface finishes.
2. Complex Geometries in Single Setup
Modern Swiss machining centers often incorporate multiple tooling stations and live tooling capabilities. This allows for complete part processing in a single setup, including turning, milling, drilling, and threading operations. The ability to perform these operations simultaneously significantly reduces production time while maintaining accuracy.
3. Material Efficiency
Swiss machining excels at working with bar stock material, feeding it through the guide bushing as machining progresses. This approach minimizes material waste compared to conventional machining methods that might require larger workpieces to be cut down to size.
4. High Production Rates
The continuous feeding mechanism of Swiss machines enables rapid production of small, precision parts. When combined with automated loading systems, Swiss machining can achieve impressive production volumes while maintaining consistent quality.
Keyword: Swiss Machining
Applications of Swiss Machining
Swiss machining has become essential across various industries that demand high-precision components:
- Medical Industry: Surgical instruments, implants, and diagnostic equipment components
- Aerospace: Fuel system components, fasteners, and sensor housings
- Electronics: Connectors, contacts, and miniature electronic components
- Automotive: Fuel injection parts, transmission components, and sensors
- Defense: Firearm components, guidance system parts, and communication devices
Choosing the Right Swiss Machining Partner
When selecting a Swiss machining provider for your complex components, consider these critical factors:
1. Technical Capabilities
Evaluate the machine shop’s equipment, including the number of axes, live tooling options, and bar feeder capacity. Modern multi-axis Swiss machines with Y-axis capability offer greater flexibility for complex parts.
2. Material Expertise
Ensure the shop has experience working with your specific material requirements, whether it’s titanium for medical implants or specialized alloys for aerospace applications.
3. Quality Assurance
Look for certifications like ISO 9001 or AS9100 and inquire about in-process inspection procedures.